CP2 FILTER Cartridges
Structure
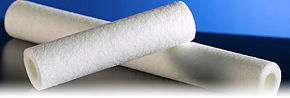
Only special bi-component polypropylene fibers developed and patented by JNC are used, and each contact point of the fibers is thermally bonded to form a rigid fiber network that has uniform porosity and high tolerance for pressure. Moreover, since spin finish is not used, there is no foaming in the initial stage of filtering liquids. Furthermore, it has a clean and rigid filter structure that utilizes the innovative filtration process technology of the CP filter.
Advantages
- Spin finish is not used, and there is no foaming at the initial stage of filtering liquids.
- The constructed super-fine polypropylene fibers developed and patented by JNC ensure finer filtration.
- The simple but clean and rigid structure utilizing state-of-the-art fiber technology allows for longer service life and higher throughputs.
- A rigid filter structure of fused fibers in a three dimensional network with a high tolerance for differential pressure is achieved.
- The diameter of the structural fibers is changed for every grade, and the grades are clearly differentiated from a nominal filtration size of 0.3μm to 350μm.
Quality
- Complies with RoHS regulations
- Complies with REACH regulations
- Production at ISO 9001 certified factory
- Production at ISO 14001 certified factory
Application
General Industry | Various plating, Water jets, Various washing water, Service water, etc. |
---|---|
Chemicals | Resins, Adhesives, Oils and fats, Catalysts, Solvents, Surfactants, etc. |
Food & Beverages | Potable water, Tea, Juices, Wine, Spirits, Soy sauce, Seasonings and soups, Vinegar, Flavoring and food additives, Syrup etc. |
Electronics | Pure water, Optical fiber cleaning, Optical films, Printed-circuit boards, Shadow masks, Lead frames, TAB, Electrolyzed copper foils, etc. |
- Our filter complies with Japanese regulations.
- Please note that regulations may vary by country, we advise you to check your local regulations prior to use.
Specifications
Media | Polypropylene |
---|---|
End Parts | Polypropylene |
O-ring | NBR, EPDM, Silicone, FKM (Fluorine Rubber) E-FKM (Encapsulated Fluorine Rubber) |
Filtration rate
Nominal | 0.3, 0.5, 0.7, 1, 3, 5, 10, 25, 50, 75, 100, 150, 200, 350 micron |
---|
Dimension
Double open ended
CP2-A3 - CP2-A7
ID | OD | Length |
---|---|---|
1.18” | 2.56” |
4.88”, 5”, 9.75”, 10”, 19.5”,20”, 29.25”, 30”, 39”, 40”
|
CP2-01 - CP2-350
ID | OD | Length |
---|---|---|
1.18” | 2.44” |
4.88”, 5”, 9.75”, 10”, 19.5”,20”, 29.25”, 30”, 39”, 40”
|
Single open ended
ID | OD | Length |
---|---|---|
0.98” | 2.76” | 10”, 20”, 30”, 40” |
Operating Conditions
Maximum Operating Temperature | 80°C (175°F) |
---|---|
Replacement Differential Pressure | 22psi |
Maximum Differential Pressure | 80psi @ 20°C (68°F) |
*depending on operating parameters
Precautions
About Absolute filter rating and Nominal filter rating
Filter rating used to be called "absolute filter rating" or "nominal filter rating", but now it is generally called "filter rating". However, there are some catalogs that are described as "absolute filter rating" and "nominal filter rating".
In actual filtration, it is almost impossible to say 100% or absolute. It is only rating of the filter maker evaluation method (original test condition)..
In the case of absolute filter rating, it is generally said by particle separation efficiency (%) or β value. i. In the case of nominal filter rating, it is determined according to different standards depending on the filter makers.
ii. There is no generally or industrially accepted definition.
Although it depends on the manufacturer and product, the actual filtration efficiency is about 50 to 98% of described rating.
(From The Association of Liquid Filtration and Purifcation Industry edited filter guidebook for users)
About hydrophilize for Pleated Filter
When using a filter material made of a hydrophobic resin such as polyolefin resin (generic name for polyethylene, polypropylene, etc.) or fluorine resin for water or aqueous solution chemicals, it is necessary to hydrophilize it in advance.
Please hydrophilize before attaching to your manufacturing process.
(Applicable products: CLEAL®POROUSFINE PTFE membrane type, PP type PF-006, PF-010) Items to be prepared:
A clean container that holds a cartridge. (Alcohol resistant PP bag, glass, etc.) Isopropyl alcohol (IPA,2-propanol) Concentration of 50% or more.
Procedure:
1. Put IPA in a clean container and slowly soak the cartridge.
At this time, do not let O-ring enter IPA as much as possible. (Because it is difficult to remove IPA in the O-ring groove)
2. When the cartridge is completely immersed, give vibration to expel the air remaining in the cartridge. 3. It is preferable to let the filter and IPA blend in, and leave it for a few minutes after air bubbling due to vibration has stopped.
After that, pull up the cartridge and wait until IPA drops to a few drops. At this time, be careful not to let IPA dry.
4. Set the cartridge in the filter housing and pour pure water to remove IPA.
It is recommended to flow about 30L at a flow rate of 5L/min. (recommend cleaning at least about 5L)
Note:
When implementing, take adequate safety measures (ventilation, protective gloves, etc.). If the cartridge becomes dry, it needs to be hydrophilized again.
Caution in the case of filtration liquid tended to be charged with static electricity (organic solvent, etc)
Synthetic resin have poor electrical conductivity and tend to be charged with static electricity due to friction. Be sure to ground the filter housing when filtering organic solvent.
Note:
When flowing organic solvent, using piping with synthetic resin material may cause electrostatic fire.
About deterioration over time of cartridge filter
Many conditions (not only chemicals, heat, light, pressure, etc.) affect the deterioration of cartridge filter.
Deterioration is promoted especially when filtering chemicals containing high temperature or oxidizing agent.
In addition, filter component made of polyester resin may be hydrolyzed by acid, alkali or hot water.
Be careful when using for a long time.
Be sure to replace your cartridge filter regularly.
Confirmation of appropriate filtration rating and filter life by observing used filter
In order to use cartridge filter effectively, it is necessary to select filter that meets the properties of contamination (particle size distribution/concentration). Observing used filter is very important.
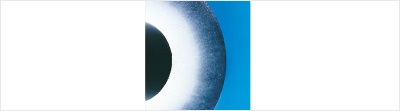
It shows the most well-balanced filtration because the filter agglomerates contaminant without spots.
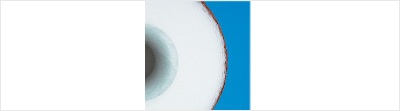
Outside layer of the filter is clogged with contaminant, conversely inside layer is clean. Micron of the filter is too small, which causes surface filtration. Advantage of depth filter does not work effectively, so filter life will be shorter. It is necessary to change the filter to larger micron or add larger micron filter into pre-processing, namely multi-step filtration.
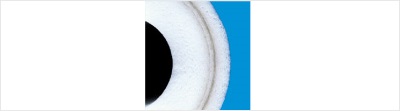
Inside layer of the filter is clogged with contaminant, conversely outside layer is clean.
Micron of the filter is too large, otherwise particle size distribution of contaminant is very narrow (monodisperse).
It is necessary to change the filter to smaller micron. In the case of monodisperse contaminant, it will be recommended to change the filter to pleated filter with a large surface area.
It is important to select appropriate cartridge filter meeting required filtration rating, but in order to use the filter life effectively (economically), it is recommended to perform multi-step filtration meeting particle size distribution of contaminant. (Example) Feed (raw) water → CLEAL®CP FILTER (large particle size filtration) → CLEAL®BM FILTER (small particle size filtration) → CLEAL®POROUSFINE (microfiltration) → target filtration
About select appropriate filter housing meeting cartridge filter
About appropriate flow speed of filter housing: In order to properly use the filter housing, it is preferable to set flow speed 0.5 to 2.5m/s less through the filter housing nozzle.
In the case of low viscosity aqueous solution, design the filter housing so that initial differential pressure of the element is 0.015 MPa or less.
Nozzle flow speed is calculated by the following formula.
Flow speed = Flow rate ÷ Pipe cross-sectional area
About filter housing selection:
Select number of elements based on the required line flow rate. In the case of low viscosity aqueous solution, select number of elements so that initial pressure loss of the element is 0.015 MPa or less from "Flow Rate-Pressure Loss diagram" of each cartridge filter. However, make sure that it is within the range of the above "appropriate filter housing flow speed". For high-viscosity liquids, past case should also be considered.
*Please contact us when selecting appropriate filter housing because it is necessary to consider liquid type and filtration condition.
How to install cartridge filter and about various filter shapes
There are two types of end face side: DOE (Double Open End, upper and lower open type) and SOE (Single Open End, one open type).
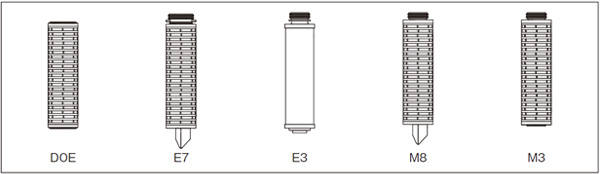
DOE seals both ends with edge seals. If the edge seal is incomplete when the filter is attached, leakage will occur from the seal part, and original performance of the filter will not be exhibited, and proper filtration will not be possible. When installing DOE type filter into filter housing with edge seal, it is necessary to select locator type, using locator with spring (metal fitting with edge formed) or using bolt fastening type locator.
For DOE type filter housing, it will be recommended to use locator type with spring to let follow swelling/shrinking of cartridge filter (thermal expansion, swelling due to chemicals) and thermal expansion of filter housing body.
Conversely, bolt fastening type locator has a difficulty in loosening bolt due to pipe vibration and sealing followability at the time of thermal expansion/contraction.
Therefore, if bolt fastening type locator is used for a long time, it is necessary to interrupt filtration, open the filter housing, and tighten the bolts.
SOE type (M3, E3, E7, M8) has O-ring on the open-side end cap.
There is end cap type with swing stop on the another side.
Since SOE type is sealed with O-ring, it will be a very suitable sealing method for high precision type filters.
* If air is trapped in filter housing during liquid flow, specified flow rate may not be obtained. In this case, air vent will be needed.
About disposal and laws
Used cartridge filter can be incinerated except for filters containing PTFE material, but after confirming the properties of the filtered chemical liquid, comply with the disposal standards of each local government (laws on waste treatment and cleaning, PRTR law) and dispose of used filters.
In addition, filter and filter housing may be regulated by laws and regulations regarding usage and individual products.
In case of lack of recognition and knowledge, unexpected accident or loss may occur. In case of filtration pharmaceuticals, high-pressure gas, dangerous substances, etc., it is necessary to use technical equipment that complies with the law.
These laws are subject to change or new enforcement, so please check the laws and regulations of the partner country when using it outside Japanese governmental authorities.
The major domestic laws and regulations are as follows.
Customers such as Pharmaceutical Affairs Law, Food Sanitation Law, Household Goods Quality Labeling Law, High Pressure Gas Safety Law, Occupational Safety and Health Enforcement Order, Fire Defense Law, Foreign Exchange and Foreign Trade Law, Waste Disposal and Cleaning Law, etc.
We are not responsible for any damage and loss with non-compliance.
In some countries, PTFE materials are regulated for contact with pharmaceuticals, foods, cosmetics, and for medical device parts.
Therefore, we do not recommend using of cartridge filter made from PTFE material in these areas.
When using PTFE material in these fields for filtration purposes, please check the laws and regulations of the partner country by yourself.
We are not responsible when using PTFE material filters in these fields.